Latin American Projects Shorten the Start-Up Cycle of Mobile Asphalt Plants Through Turnkey Solutions
- Aimix maquina
- 24 jun
- 3 Min. de lectura
Across Latin America, road construction and infrastructure development are moving at an accelerated pace. From rural access improvements in Colombia to urban highway upgrades in Peru and Brazil, contractors are under pressure to deliver quality results faster than ever. A major bottleneck in project timelines has traditionally been the start-up and commissioning period of asphalt production equipment. However, the rise of turnkey solutions—especially for mobile asphalt plant(planta de asfalto movil) setups—has dramatically shortened this start-up cycle.
Instead of sourcing and assembling equipment piece by piece, contractors are now turning to suppliers who deliver complete, ready-to-install systems with integrated services. These turnkey packages are not only speeding up project launches but also improving equipment reliability and reducing the risk of costly delays.
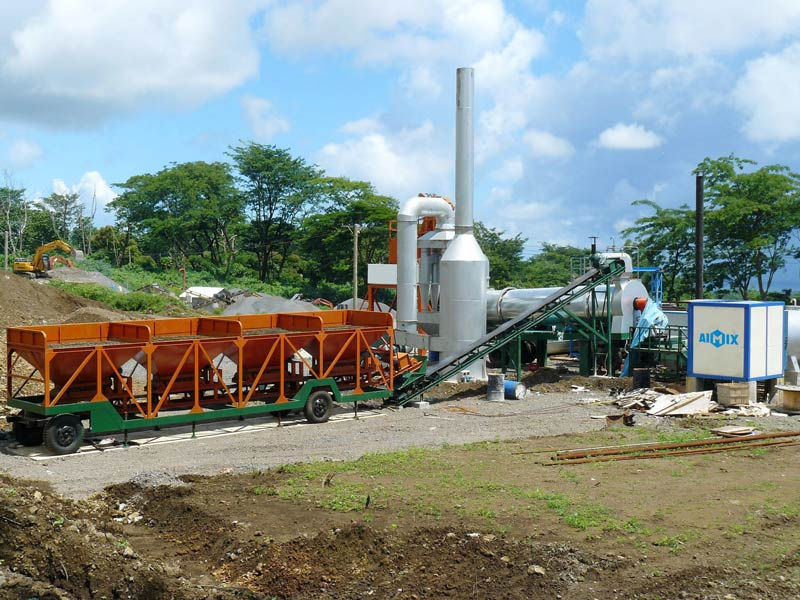
Why Turnkey Solutions Are Gaining Momentum in Latin America
The logistical and operational challenges of infrastructure projects in Latin America are well known: rugged terrain, remote sites, customs delays, and limited access to skilled labor. For many contractors, traditional procurement methods—where each component of an asphalt plant is sourced and installed separately—are simply too slow and complex.
A turnkey solution changes this dynamic. The entire plant, whether a batch type asphalt plant or a mini asphalt plant(mini planta asfalto), is pre-configured, pre-wired, and factory-tested before shipment. Once it arrives on site, the supplier’s technical team handles installation, commissioning, and staff training, often within just one to two weeks.
This model is ideal for government-funded fast-track projects or private contractors working on tight construction seasons in mountainous or tropical regions.
Components of a Turnkey Mobile Asphalt Plant Solution
Pre-Integrated Equipment and Controls
A true turnkey mobile asphalt plant comes with every module pre-aligned—aggregate feeders, drying drum, burner, mixing tower, control system, and even bitumen storage. All electrical systems are connected in advance, and the plant undergoes a dry test run at the factory.
This ensures that once the equipment is delivered, it can be assembled quickly with minimal technical adjustments. The risk of on-site wiring errors, mechanical mismatches, or calibration issues is nearly eliminated.
Logistics and Site Planning
Suppliers offering turnkey solutions often include logistics planning in their service. This covers not only sea and land transportation but also advice on plant placement, foundation requirements, and local permitting. For remote sites, where moving heavy machinery is a challenge, these logistical insights are invaluable.
Installation and Training Support
One of the biggest advantages of turnkey projects is the inclusion of on-site technical support. The supplier typically sends engineers to oversee installation, calibrate systems, and run test batches. They also provide training for local operators, ensuring that the production team is ready to take over as soon as the plant is commissioned.
This is especially beneficial for crews unfamiliar with newer automation systems or when working with a batch type asphalt plant(planta de asfalto estacionaria) that requires specific mix designs and cycle times.
Benefits of a Faster Start-Up Cycle
Rapid Project Mobilization
In regions with short dry seasons or strict public infrastructure deadlines, being able to start asphalt production in just a few days can make or break a project. A turnkey mobile asphalt plant solution allows contractors to start laying pavement weeks earlier compared to traditional setup methods.
Lower Initial Labor and Overhead Costs
Turnkey setups reduce the need to hire multiple subcontractors for civil works, electrical installation, or calibration. This helps control start-up costs and simplifies project management. Contractors can reallocate those resources toward core construction tasks like roadbed preparation and logistics.
Quality Assurance and Performance Stability
Since the equipment is factory-tested and installed under the guidance of the supplier’s engineers, the initial production quality is usually much higher. This reduces the need for rework, ensures compliance with road authority standards, and builds contractor credibility.
Turnkey systems also allow for smoother transitions between project sites. For example, a mini asphalt plant installed using this method can be easily relocated to a secondary project within days, maintaining continuous workflow across a contractor’s portfolio.
Conclusion
As Latin American countries continue to invest heavily in transportation infrastructure, the demand for faster, more reliable construction workflows has never been higher. Turnkey solutions for mobile asphalt plant deployment offer a smart response to this challenge by dramatically reducing start-up cycles and simplifying installation.
Whether it's a fully equipped batch type asphalt plant for a national highway or a compact mini asphalt plant for rural access roads, turnkey setups ensure that production starts on time, operates efficiently, and delivers consistent results. For contractors aiming to stay competitive in a rapidly evolving market, this approach is not just convenient—it’s essential.
Comments